Fluoroplastic magnetic pumps replace dynamic seals with static seals, keeping the flow components completely sealed. This solves the problems of leakage, spouting and dripping that cannot be avoided by mechanical seals in other pumps. The magnetic pump selects engineering plastics, corundum ceramics and stainless steel with corrosion resistance and high strength as manufacturing materials. Therefore, it has good corrosion resistance and can prevent the conveyed medium from being contaminated. The magnetic pump has a compact structure, beautiful appearance, small size, low noise, reliable operation and convenient maintenance.
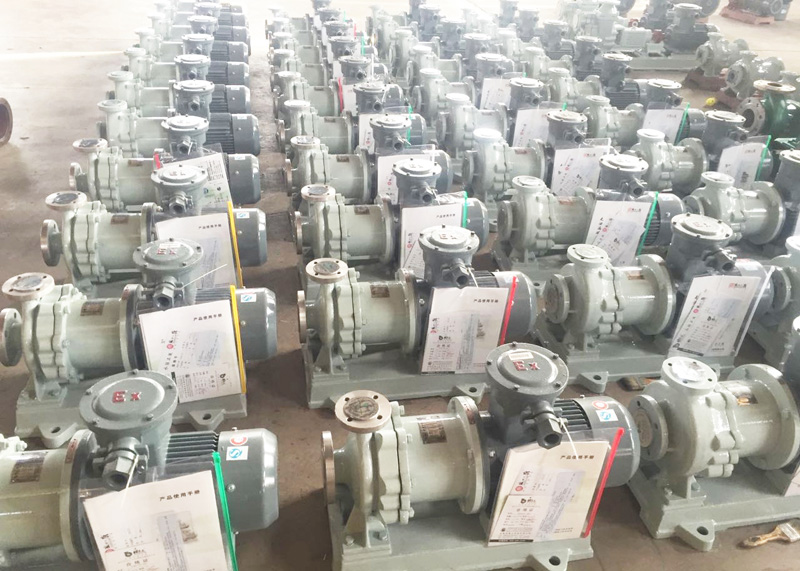
If no protective measures are taken for the flange of the fluoroplastic magnetic pump and it is exposed to a corrosive environment or contaminated industrial atmosphere, the corrosion rate will be very fast. In addition, due to the complex geometric shape of the flange connection, gap corrosion between the two flange faces and galvanic corrosion between different metals are prone to occur, which will seriously damage the integrity of the pipeline system. So how can flange connections prevent corrosion?
- Mechanical solutions: mainly by using protective covers and clamps to seal the gaps between flanges and flange faces, usually made of stainless steel or plastic with rubber sealing strips. This protection method is less flexible and requires storage of covers or clamps that match the size of various flanges completely.
- Thermoplastic solutions: Thermoplastics are essentially a kind of waxy fusible polymer heated at high temperature, which is sprayed onto the surface of the base material through professional thermoplastic equipment. The advantage of this protection method is that it can be remelted and reused, saving costs. However, this method still requires hot work, professional equipment and construction services. Although it can be reused, it is not easy to open and seal during maintenance.
- Tape or semi-solid anti-corrosion tape solutions: Rolled tapes (such as petrolatum tapes, wax or elastic polymer bandages) are protected by winding on the surface of the base material. Due to the good water resistance of semi-solid polymers, this protection method can provide reliable anti-corrosion protection.
- Maintenance paint solutions: Maintenance paint is a hard film that can be directly bonded to the base material, generally epoxy or polyurethane coatings. There are many corners and edges on the flange. Due to the edge thinning effect, conventional paint systems are difficult to effectively cover the edges. Although thickening the coating will solve the edge protection problem, it will also seal the fasteners and make them unable to be disassembled during subsequent maintenance. In addition, operating the bolt will damage the coating and must be repainted after maintenance.
- Polymer sealing bag solutions: The sealing bag can completely wrap the flange. Its composition consists of low-permeability polymers, corrosion inhibitor vapors and desiccants. It is easy to install, but the two ends of the bag are only sealed with tape instead of using a durable and effective mechanical bond. There is a large area of steam space inside the bag, which is easy to gather a lot of water, and the corrosion inhibitor will also be consumed over time.